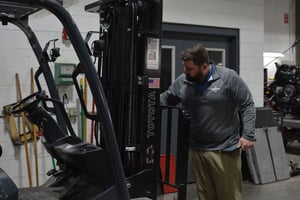
OSHA's Top 10 Violations of 2024: A Focus on Worker Safety
The Occupational Safety and Health Administration (OSHA) has released its annual list of the top 10 most frequently cited standards for fiscal year 2024. This list highlights areas where employers may need to improve their safety and health programs to protect their workers.
PARTNER SPOTLIGHT
Dealer Management System, Computer Technology, Media/Advertising, Automotive Auction, F & I/Aftermarket Products, Automotive Technology Training & Compliance
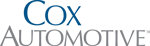
Computer Technology, Automotive Shop Equipment, Environmental Services
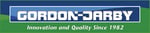
F & I/Aftermarket Products, Automotive Technology Training & Compliance, Environmental Services
.png?width=150&name=corp_logo_horz_on_light_with_trademark_symbol_1200w%20(002).png)
Unpacking the Top 10
Violations we’ve seen at NHADA member businesses are displayed in red.
How Do NHADA Members' Violations Compare to OSHA’s Top 10?
During our audits of NHADA members, we frequently identify several of the same violations listed in OSHA’s Top 10. Below are the violations we most commonly encounter:
- Machine Guarding (1910.212): Issues include missing guards, missing shields, missing tool rests, or improper tool rest adjustments on bench grinders.
- Hazard Communication (1910.1200): Secondary containers are often not properly labeled with the chemical name. All containers holding chemicals must be labeled. Safety Data Sheets (SDS) are sometimes out of date or missing. Every chemical used in service and parts areas must have an updated SDS.
- Respiratory Protection (1910.134): Problems include incomplete medical questionnaires, uncompleted fit tests, and improper respirator storage. Employees using half-face dual cartridge respirators must complete a medical questionnaire, which is reviewed by a medical professional to ensure they are fit to wear the respirator. Afterward, a fit test and training must be conducted to ensure a proper seal and teach the employee how to use, maintain, and store the respirator properly.
- Powered Industrial Trucks (1910.178): Common issues include incomplete forklift inspections, which should be conducted and documented before each shift, operators not wearing seatbelts, which must be worn at all times while operating, and incomplete training or evaluations for forklift operators. Training must be completed before operating a forklift, and recertification is required every three years or after an incident or near miss.
- Personal Protective Equipment - Eye and Face Protection (1926.102): Employees often fail to wear safety glasses when required, such as when working under vehicles or using pneumatic tools like air guns or impact guns.
The Impact of Non-Compliance
Non-compliance with OSHA standards can result in serious consequences, including:
- Injuries and Illnesses: Non-compliance can lead to workplace injuries and illnesses, which can have a devastating impact on workers and their families.
- Fines and Penalties: OSHA can impose significant fines on employers who violate safety and health regulations.
- Lost Productivity: Accidents and illnesses can disrupt operations and reduce productivity.
- Damage to Reputation: Negative publicity associated with workplace safety violations can damage an employer's reputation.
Promoting Workplace Safety
Employers can take several steps to reduce workplace hazards and prevent injuries and illnesses:
- Develop a Strong Safety Culture: Encourage a culture of safety by prioritizing safety in all aspects of the business.
- Provide Adequate Training: Train employees on safety procedures, hazard recognition, and emergency response.
- Conduct Regular Inspections: Regularly inspect workplaces to identify and correct hazards.
- Invest in Safety Equipment: Provide employees with the necessary personal protective equipment (PPE) to protect them from hazards.
- Encourage Employee Participation: Involve employees in safety committees and encourage them to report hazards.
By prioritizing workplace safety, employers can create a safer and healthier work environment for their employees and protect their business from potential liabilities.
If you are interested in improving your workplace safety culture, or have questions on the above, please contact safety@nhada.com or call 603-224-2369.