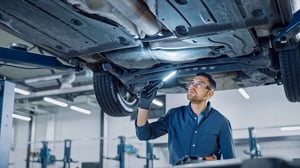
Automotive Lift Safety Need to Knows
Compliance with the ANSI Auto lift safety standard and the implementation of auto lift safety best practices remain critically important!
The requirements of the ANSI standard, (which can be cited and enforced by OSHA) are outlined in ANSI/ALI ALOIM:2008 published by the Automotive Lift Institute (ALI). If you have lifts in your facility, a copy of this standard should be with the paperwork kept with the lifts. If you need a copy of the standard contact your lift service provider or ALI.
PARTNER SPOTLIGHT
Dealer Management System, Computer Technology, Media/Advertising, Automotive Auction, F & I/Aftermarket Products, Automotive Technology Training & Compliance
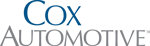
Computer Technology, Automotive Shop Equipment, Environmental Services
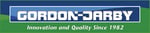
F & I/Aftermarket Products, Automotive Technology Training & Compliance, Environmental Services
.png?width=150&name=corp_logo_horz_on_light_with_trademark_symbol_1200w%20(002).png)
F & I/Aftermarket Products, Financial Services, Automotive Technology Training & Compliance
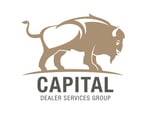
Owners of auto lifts need to ensure the following:
Training: Operators are trained in the safe use and operation of the lift as well as how to perform manufacturer recommended routine (daily, weekly, monthly) inspections and maintenance. Lastly, how to report problems with auto lifts.
Annual Inspections: Perform annual lift inspections utilizing a qualified lift inspector and make necessary repairs.
Record Keeping: Records of all training, inspections, maintenance and repairs must be maintained and easily accessible.
Proper Paperwork: Make sure all lifts have lift paperwork including
-
- manufacturer’s operation manual
- lift safety instructions and;
- vehicle pick up points reference material.
The best way to comply and ensure auto lifts are utilized safely in your operation is to implement auto lift safety best practices, these include:
Leadership: Assign a person responsible for the program, typically the service manager or shop foreman.
Servicing: Establish a working relationship with a reputable lift service company.
Record Keeping: Establish a process (manual or electronic) for recordkeeping of all training, inspection, and repairs.
Training: Train all employees utilizing NHADA’s Teamwork Approach to Auto Lift Safety DVD and a hands on portion covering all manufacturers required information for each lift they utilize. The hands on portion should be conducted by your lift service provider or an individual that is trained and certified to conduct the training. All shops should have an individual attend a 'Train the Trainer' class for instructing new hires.
Create Guidelines: Develop a policy requiring compliance with all aspects of auto lift safety with a focus on operator’s appropriate use of all safety features/work practices at all times. This policy should be posted in the work area.
Automotive lift hazards are substantial and deserve due diligence to minimize the potential for disaster. NHADA Loss prevention is available to assist you throughout the process. We work closely with our NHADA Auto Lift Service Bronze Partners, Lift Works Corp/Sullivan Tire and Mike’s Equipment and Repair to coordinate the operator training. NHADA’s Teamwork Approach to Auto Lift Safety Video is available free to NHADA WCT members!
Email Brian Duplessis or call 800-852-3372 for more information